This 150W BLDC motor offers a cost-effective and efficient solution for electric vehicle applications, operating on 12V DC with a 3000 RPM rated speed. It features a holding torque of 0.48 Nm and a peak torque of 1.43 Nm, along with a 3-phase design and an included controller for smooth, low-maintenance performance. With an IP54 protection rating, it's suitable for dusty and light water-exposure environments, and customization options like integrated brakes and gearboxes are available for varied applications.
Specification
Model |
BLDC-D2BLD150-12A-30S |
Rated Power |
150W |
Rated Voltage |
12V DC |
Matched Controller |
BLDC-KVD2412N |
Rated Current |
15.63A |
Phase |
3 phase |
Rated Torque |
0.48 Nm |
Max. Torque |
1.43 Nm |
Rated Speed |
3000 rpm for standard (or 2000 rpm when matching the worm gearbox) |
No-load Speed |
/ |
No-load Current |
<1.5A |
Working Efficiency |
71% |
Square Flange Size |
60 mm |
Insulation Grade |
F |
Protection Grade |
IP54 |
Motor Lead Length |
1 meter |
Certificate |
CE, RoHS, ISO |
Weight |
3 kg |
Note: Power, voltage, speed, shaft, motor length, and motor lead of BLDC motors can be customized.
Features
- Stable Speed Control: The 150W BLDC motor maintains a set speed by continuously comparing feedback signals and adjusting voltage, ensuring consistent performance even with load changes.
- Compact & High Power: Uses a permanent magnet rotor in a 3 phase design, delivering a thin profile with high power density.
- Wide Speed Range: It offers a broader speed control range than AC motors and inverters, providing strong torque from low to high speeds without brushes.
- Energy Efficient: Permanent magnet rotor reduces rotor losses, cutting power consumption by over 20% compared to variable frequency induction motors, supporting energy savings.
- Built-in Protection: Brushless DC motor includes safety features to protect the equipment system.
Dimension (Unit: mm)
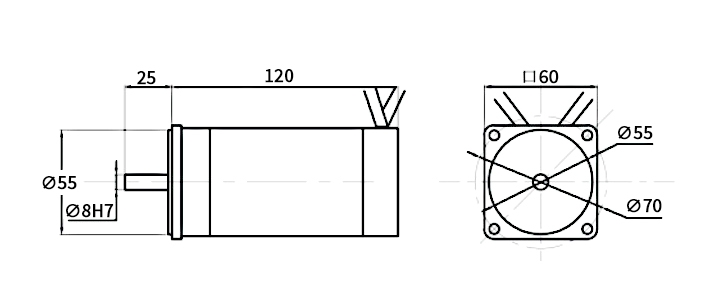
Speed - Torque Curve
- Instantaneous maximum torque line: This torque represents the peak load impact when the motor starts. If exceeded, the driver’s over-current protection will trigger, stopping the motor.
- Short-time operation area: The BLDC motor can operate briefly within this torque range at various speeds. Prolonged operation may cause overheating, potentially leading to motor shutdown or damage.
- Rated operating torque line: At different speeds, this torque level is the electric DC motor’s rated load, allowing long-duration operation without issues.
- Continuous operating area: The brushless motor can run continuously within this zone at varying speeds, maintaining stable operation.
Line Define
Power Wire |
Hall Wire |
Red |
U |
Red |
5V |
Yellow |
V |
Black |
GND |
Black |
W |
Blue |
Hu |
Green |
Hv |
White |
Hw |
Applications
Q: Why do BLDC motors require electronic commutation?
A: Traditional brushed motors use mechanical brushes and commutators to switch the direction of current, which leads to friction, heat generation, and wear over time. In contrast, BLDC (Brushless DC) motors use electronic commutation, utilizing Hall sensors or back electromotive force (EMF) to replace mechanical components. This electronic method eliminates the friction and wear associated with brushes, significantly improving efficiency, reducing heat, and extending the motor’s lifespan.