3-phase BLDC motor operates on 12V, 24V, 36V, or 48V DC, offering 300W of rated power, 3000 rpm speed, and 0.96Nm torque. Featuring an 86mm square flange, this brushless motor ensures precise torque and speed control, delivering high efficiency and excellent controllability.
Specification
Model |
BLDC-D5BLD300 |
Rated Power |
300W |
Rated Voltage |
12V DC |
24V DC |
36V DC |
48V DC |
Matched Controller |
BLDC-KVD2412N |
BLDC-BLD750 |
BLDC-BLD4850 |
BLDC-BLD750 |
Rated Current |
31.25A |
15.6A |
10.42A |
7.81A |
Phase |
3 phase |
Rated Torque |
0.96 Nm |
Max. Torque |
2.87 Nm |
Rated Speed |
3000 rpm for standard (or 2000 rpm when matching the worm gearbox) |
No-load Speed |
/ |
3300 rpm |
/ |
/ |
No-load Current |
<7.2A |
<6.13A |
<3.5A |
<4.61A |
Working Efficiency |
71% |
85% |
Square Flange Size |
86 mm |
Insulation Grade |
F |
Protection Grade |
IP54 |
Motor Lead Length |
1 meter |
Certificate |
CE, RoHS, ISO |
Weight |
6 kg |
Note: Power, voltage, speed, shaft, motor length, and motor lead of BLDC motors can be customized.
Features
- Stable Speed Control: The 12V/24V/36V/48V BLDC motor maintains a consistent speed by comparing a feedback signal from the motor's speed to adjust the applied voltage. This ensures the speed remains stable even with load changes, providing smooth, instant adjustments for precise control.
- Compact & High Power: 3-phase DC motor uses a permanent magnet brushless rotor, achieving both a compact design and high power output.
- Wide Speed Control Range: The speed control range of the 300W BLDC motor surpasses that of AC motors with inverters. Unlike AC motors that face torque limitations at low speeds, this brushless motor offers continuous torque across a wide speed range, from low to high speeds.
- Energy Efficient: With a permanent magnet rotor, the brushless motor minimizes rotor losses, reducing power consumption by over 20% compared to 3-phase induction motors with frequency control, contributing to overall energy savings.
- Equipped with Protection Function: The high-speed BLDC motor includes protective features to safeguard the equipment system’s safety during operation.
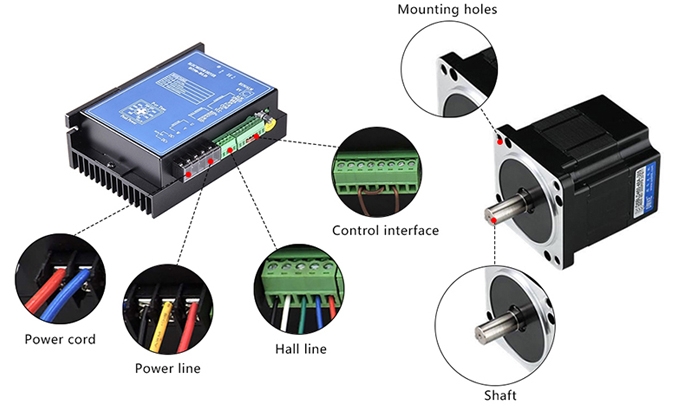
Dimension (Unit: mm)
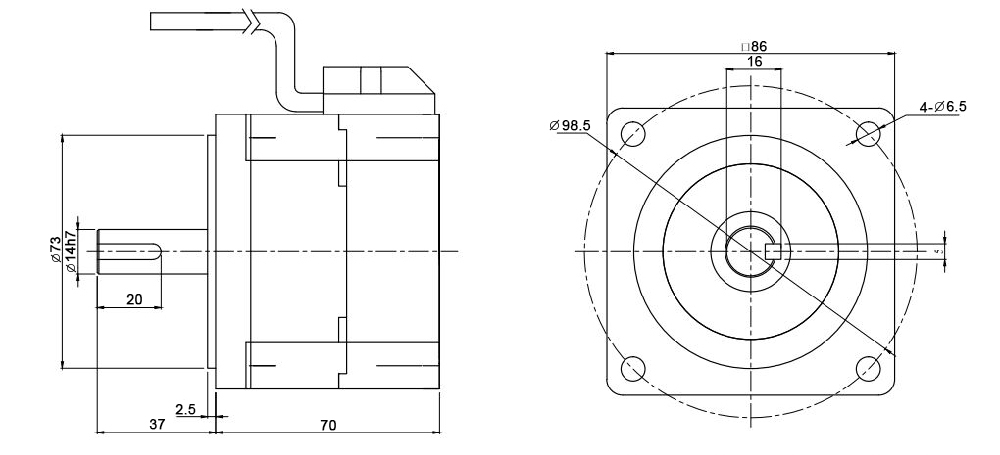
Speed - Torque Curve
- Instantaneous maximum torque line: The maximum torque briefly affects the load during motor startup. Exceeding this torque triggers the over-current protection in the driver, causing the motor to stop.
- Short-time operation area: The motor can operate for short durations within this torque range at varying speeds. Prolonged operation in this area may lead to excessive heat, potentially causing the motor to stop or even burn out.
- Rated operating torque line: The rated torque of the motor is maintained at different speeds, allowing for long-term operation at this torque.
- Continuous operating area: The BLDC motor can run continuously within this zone at various speeds without overheating or damage.
Line Define
Power Wire |
Hall Wire |
Red |
U |
Red |
5V |
Yellow |
V |
Black |
GND |
Black |
W |
Blue |
Hu |
Green |
Hv |
White |
Hw |
Applications
Q: What causes a BLDC motor to overheat?
A: A BLDC motor may overheat due to overloading, poor ventilation, or running at voltages and currents beyond its rated limits. Prolonged operation in high-torque zones intended for short durations, or issues with the motor controller, can also lead to excessive heat. Ensuring proper cooling, correct driver settings, and operating within specified limits helps prevent overheating.