24V/48V 400W BLDC motor delivers 3000 rpm speed and 1.3 Nm torque, offering precise control of torque and speed. With an 80mm square flange, this brushless motor ensures high efficiency and smooth performance, making it ideal for various applications.
Specification
Model |
BLDC-D5BLD400 |
Rated Power |
400W |
Rated Voltage |
24V DC |
48V DC |
Matched Controller |
BLDC-BLD750 |
Rated Current |
21.3A |
10.6A |
Phase |
3 phase |
Rated Torque |
1.3 Nm |
Max. Torque |
2.54 Nm |
Rated Speed |
3000 rpm |
No-load Speed |
3600 rpm |
Working Efficiency |
85% |
Square Flange Size |
80 mm |
Insulation Grade |
F |
Protection Grade |
IP54 |
Motor Lead Length |
1 meter |
Certificate |
CE, RoHS, ISO/TS16949 |
Weight |
2.4 kg |
Note: Power, voltage, speed, shaft, motor length, and motor lead of BLDC motors can be customized.
Features
- Stable Speed Control: The 400W BLDC motor maintains a set speed by continuously comparing feedback signals and adjusting voltage, ensuring consistent performance even with load changes.
- Compact & High Power: Uses a permanent magnet rotor in a 3 phase design, delivering a thin profile with high power density.
- Wide Speed Range: It offers a broader speed control range than AC motors and inverters, providing strong torque from low to high speeds without brushes.
- Energy Efficient: Permanent magnet rotor reduces rotor losses, cutting power consumption by over 20% compared to variable frequency induction motors, supporting energy savings.
- Built-in Protection: Brushless DC motor includes safety features to protect the equipment system.
Dimension (Unit: mm)
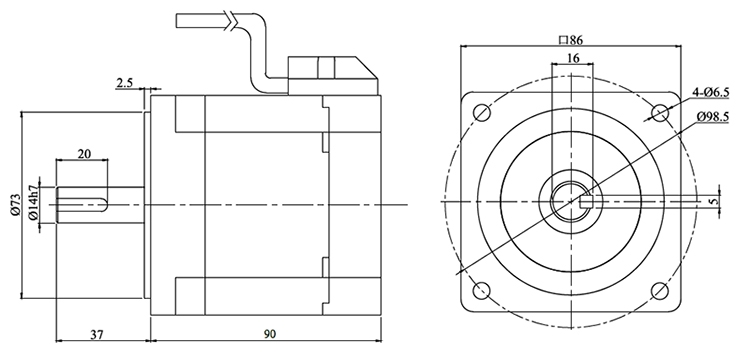
Line Define
Power Wire |
Hall Wire |
Red |
U |
Red |
5V |
Yellow |
V |
Black |
GND |
Black |
W |
Blue |
Hu |
Green |
Hv |
White |
Hw |
Applications
Q: What happens if a brushless motor gets wet?
A: If a BLDC motor gets wet, it can lead to several issues, including corrosion, electrical shorts, and reduced performance. While some brushless motors can operate underwater for short periods, they are not typically designed for prolonged exposure to water, especially saltwater. Potential Problems:
- Corrosion and Rust: Water, especially saltwater, can cause rust and corrosion on metal components like bearings, magnets, and other internal parts.
- Electrical Shorts: Water can create a path for electricity to flow where it shouldn't, potentially causing short circuits and damaging the motor's electronics. Reduced Performance: Moisture can interfere with the motor's operation, leading to inefficiency, irregular operation, or complete failure.
- Bearing Failure: The bearings in a BLDC motor are particularly susceptible to water damage, as they are often not made of stainless steel or a rust-resistant grade.
- Magnet Damage: In some cases, prolonged exposure to water can affect the magnets within the motor, potentially causing them to lose strength or become damaged.